

Pick-and-place Surface Mounting
Essemtec Cobra
These machines are used to place components onto printed circuit boards at high speeds and with great precision. The operations are so delicate and precise; I think the placement head looks like a little ballerina as it rotates between nozzles and tiptoes ever so delicately across the circuit board, placing its little footsteps carefully and leaving shiny metal components in its path. The machine that you see here is called a "gantry-style" pick-and-place machine because it uses a gantry, which is basically a big support that allows the placement head to move freely around above the components being worked on. The previous iteration of pick-and-place machines from the 80s and 90s used something called a "chip shooter", which looks really cool in action also. They were big rotating turrets that were fed tiny electrical components and essentially would just shoot them out onto the circuit board at high speeds. Chip shooters moved the circuit board around instead of the turret, and in order to achieve the speeds required for mass manufacturing they would have to jerk those circuit boards around pretty hard. This meant that the chip shooters could only be used to place very lightweight components that wouldn't get thrown off the bucking bronco of the "x-y table" (that's the thing that circuit board is moved around on, because its movement is mapped along the x-y axes).
But the thing about those older chip shooters is that they would usually have to hand off the circuit board to a gantry-style precision placer anyway. Because of the limitations of moving the board around on an x-y table, and the complexities of loading large or oddly-shaped components into the continuous "tape-and-reel" feeders, an earlier form of our modern pick-and-placers would be used to place these components with more precision. Eventually, mechanical engineers just decided to scrap the chip shooters altogether and integrate their faster feeding system (the tape-and-reel feeder, which is like a little conveyor belt) into the pick-and-place machine for those smaller identical components that previously would have been placed with the chip shooters. "Bulk feeders", which are loaded with trays of components that are then picked up and placed, remained in use for the large or odd-shaped components, and voila!--an integrated pick-and-place machine that can do it all. This is far more energy-efficient because it's just one machine instead of two, and I would guess that it's much easier to repair because you can troubleshoot more easily when there are fewer workflows involved in the process. Mostly though, I just like to watch them do their thing.
This particular machine is the Essemtec Cobra, which I really like because of its cool black and red stylings and its complex conveyor system which moves the circuit board around as it goes from one part of the machine to another.
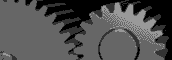
Commercial Glass Blow-Molding
Glass bottle manufacturing plant
This whole webpage actually came about in large part because of this manufacturing process. When I received some cool new glassware in the mail, I mused to a friend about how it might have been produced. He told me about a clip he remembered from the TV show "How It's Made" where they showed a glass bottle factory. The footage was so beautiful and hypnotic--I love how the molten glass gobs get shot down those transport lines. It looks so industrial and cyberpunk, the way the glowing orange reflects off the metallic machines as it moves. I wanted to watch this clip on loop with some cool music, so here we are doing just that :)
Here's how these things work: just above this machine is a massive vat of molten glass. And I mean MASSIVE. People who work at these plants talk about how mesmerizing it is to look into the windows on the vats and see a small ocean of molten glass. The molten glass is extruded into gobs, which are cut into the exact right size to become a bottle. The gobs are then shot through a transport system into two-part molds. This is where the process of "blow-molding" begins. Usually in order to manufacture a bottle or cup, you have to use a three-part mold: two parts for each side of the vessel and a third for the inner cavity. (If you are curious to know more about the way this is done, this website will tell you everything you could ever want to know about bottle manufacturing.) The innovation with blow-molding machines is that they mimic a mouth-blowing process, allowing the third part of the mold to be replaced by air. Instead of forcing the molten glass into a three-part mold, the glass is poured into a two-part mold and then a burst of hot air forces the glass into shape. This also allows the bottle to be released from the mold more easily.
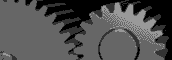
CNC Wire Bending
AIM AFE-2D6 ULTRA
Look at this wire bender going fucking crazy! I love the sounds it makes and its little jerking motions. I like wire benders because their operation seems so effortless; it looks like they are expending barely any energy and yet they're popping out hooks and springs like there's no tomorrow. This is partially due to the extruder; I think that if the wire is coming out of there fast enough you don't really have to apply much energy to redirect its motion.
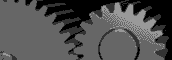
Automated Packing
Schubert Lightline Cartonpacker
I LOVE SCHUBERT MACHINERY! I will shout it from the mountaintops. I think these things are so beautiful. If you ever get really stoned and want to enter a trancelike state, just pull up the Schubert company's Youtube channel. They're a German company that makes the most beautiful machines; I love their bright blue and white colorway and the modularity of their designs (the design of their machines is such that you can construct an assembly line over time, as the machines will work together to transport items between them as more are added on).
What I love about this specific machine, the Lightline Cartonpacker, is how intentional the movements of the robotic arms appear to be as they move the boxes from place to place. They even appear to hesitate before performing more delicate operations like sealing the adhesive on the underside of the boxes, as if they are carefully considering how much force to apply. The whole thing just looks so efficient and thoughtful at the same time. The boxes come out of this machine perfectly packaged without a scratch or a dent anywhere. Such a gentle robot.
I also love this video of a Schubert pick-and-place packer, which operates similarly to the pick-and-place machines we talked about earlier--only instead of breadboards, this one operates on actual bread. The "pneumatic gripper", which uses gentle suction to lift and place objects, is so gentle with these biscuits. I can't imagine the level of precision that goes into calculating the exact force of suction needed to lift the biscuits without breaking them. I think the suction is filtered through a sponge-like material on this machine, but I could be mistaken. I just think it's so satisfying to watch.
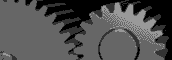
Progressive Die Stamping
Scandic Progressive Die
Progressive die stamping is kind of self-explanatory; it basically involves a progression of "dies", which is the broad term for any machine tool that uses a press to cut or form material. Metal sheet is fed along the row of dies, which bends or stamps it into different shapes. I love the big heavy thunking sound the machine makes as it does its thing. Some of these bad boys can produce hundreds of finished metal parts per minute, which amounts to several million(!) per year. The motion of the machine also makes me kind of horny, but we're not here to talk about that.
This particular machine is made by Scandic.